1983年 世界初の「CFRP製カスケード」を開発
産業構造の転換期に、炭素繊維複合材料に着目
精密ポンプの流体技術をコアテクノロジーとする日機装が、航空宇宙分野へ参入する契機となったのは、1981年から取り組み始めた「新素材」の開発でした。
この時期、二度にわたる石油危機を経験した日本の産業界は、「大量生産型」から「多品種少量生産型」へ、さらには「高付加価値型」へと事業構造の転換を図っていました。
人工腎臓装置をはじめとする医療器部門の高度成長が一段落した当社も、バイオテクノロジー、エレクトロニクス、新素材といった領域での技術革新を模索しており、なかでも「軽くて強い炭素繊維」という先端素材に、大きな将来性を見出しました。そして、炭素繊維を強化材として樹脂に複合させた「炭素繊維強化プラスチック(CFRP)」の開発に成功したことから、航空宇宙分野での本格的な事業展開が始まります。
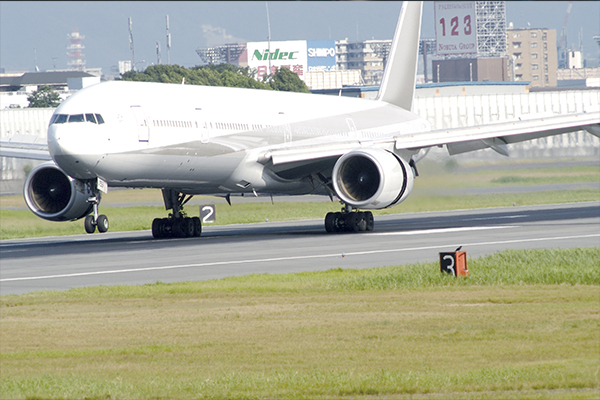
“炭素繊維”の工業化が航空業界の未来を拓く
航空宇宙市場への進出をめざす日機装にとって、最初に訪れたチャンスは、1981年に米国ボーイング社(世界最大の航空宇宙機器メーカー)から依頼された、「グラファイトウィスカー(微細な炭素繊維)」の製造でした。軽くて強い炭素繊維は、従来の金属素材に替わる軽量素材として、産業界から大きな期待が寄せられていましたが、当時は生成技術も、工業化も確立していませんでした。
当社は製造にあたり、さまざまな方法を試しましたが、最終的に実験を成功に導いたのは、当社が特許を持つ「流動気相法」という世界初の製造方法でした。これは、たとえば炭素繊維であれば、従来比200倍という高い生産性を実現するもので、この快挙は日経新聞のトップを飾るほどの注目を集めました。当社は、素材の開発にとどまらず、“素材の工業化”にも大きな展望を開いたのです。
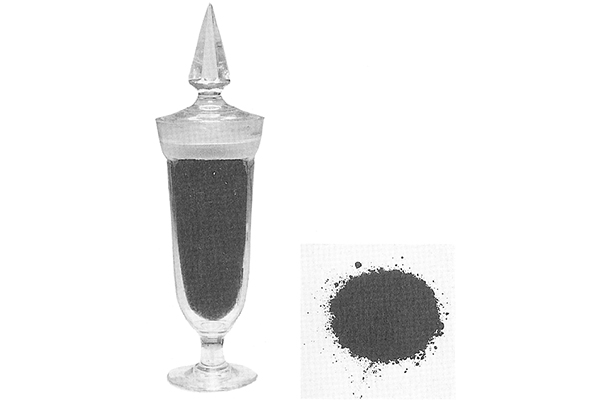
世界で初めて、カスケードのCFRP化を実現
軽さと強さに優位性を持つ炭素繊維ですが、その半面、加工が非常に困難という難点がありました。ところが、日機装の炭素繊維複合材ビジネスの突破口を開くチャンスが不意に訪れます。米国ロアー社(航空機エンジンの収容部であるナセルの大手メーカー)からの「炭素繊維で、軽くて耐久性の高いカスケード(逆噴射装置部品)を作れないか」という打診があったのです。
この新たな挑戦は文字どおりゼロからのスタートであり、当社は製造工程の構築から着手し、さまざまな試行錯誤を繰り返しました。そして、1983年に世界初となるCFRP製のカスケードを開発し、翌年に米国連邦航空局の認証を得て、航空機メーカーへCFRP製カスケードの供給を開始しました。以来、日機装のカスケードは、航空機の標準仕様として認められ、2大航空機メーカーのボーイングとエアバスの主要機種から各国のリージョナルジェットまで、あらゆる機種で採用され、現在の世界シェアは9割を超えています。
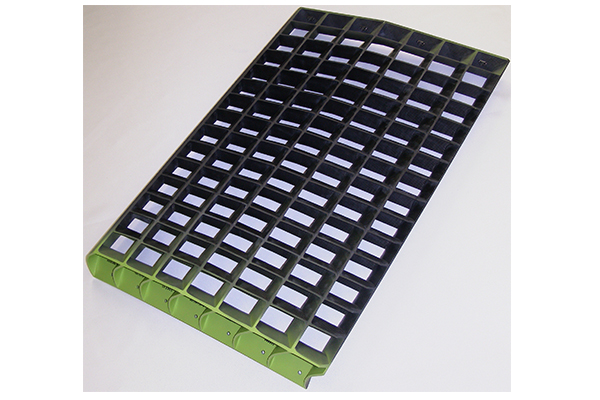
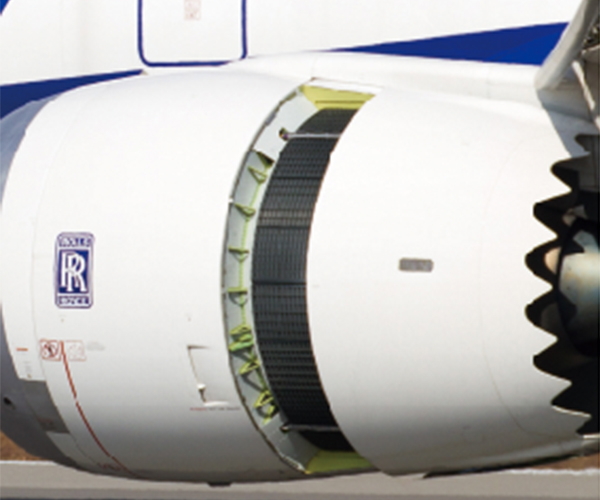